
For
Contractors
Investigating and resolving damp
issues in occupied houses
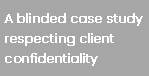
This housing development had already been a problem site for some time when we were called-in. Residents were experiencing damp inside their houses and render was falling off the external walls. The client’s normal aftercare process wasn't resolving the issues, despite everyone’s best intentions and actions.
​
The development had used an innovative build process involving Light Steel Frame (LSF), so traditional remediation methods were simply not getting to root of problem. The client wanted to resolve the issue properly and fully, rather than just keep patching things over.
​
They decided they needed the expertise of a professional who understood LSF in detail, which is when Westbrook & Bell became involved. Charles Westbrook’s experience of LSF was exactly what the client needed.
​
Our task was to identify what was causing the issues and develop a practical solution which could be implemented whilst the home owners were still in residence.
​
Combining in-depth on-site investigations with a thorough review of the original design details, we identified a combination of issues which had come together to cause the problems residents were experiencing. They included a variety of poor detailing issues at design stage, sub-par workmanship on site, and a possible problem with one of the construction materials, which has since been withdrawn by the supplier.
​
This combination of issues created the conditions where condensation within the wall build-up was inevitable.
​
Our resolution included revisions to the problem details and a change of external wall finish, whilst retaining the original 'look' of the individual properties and the development as a whole.
The client wished to retain the same suppliers as had been originally used, so we worked with them to assess potential replacement materials and identify the right options. We produced a detailed list of appropriate materials to correct the defects, right down to the last screw; then created a sequential work schedule encompassing the detailing and the external wall works, to ensure the remediation works were completed with optimum efficiency and efficacy.
During the remediation process we undertook site visits to quality check the works, ensuring that all the details were in accordance with the manufacturers’ instructions, thus meeting warranty conditions.
Throughout the entire process, we worked closely with the client, supporting their Technical and Site Teams to achieve what was needed.
​
The buildings now have a properly balanced through-wall construction.
​​
​The through-the-wall breathing is improved, and the external render is no longer delaminating: it still looks sharp 12 months after the works were completed.
​​

The external render finish was spalling
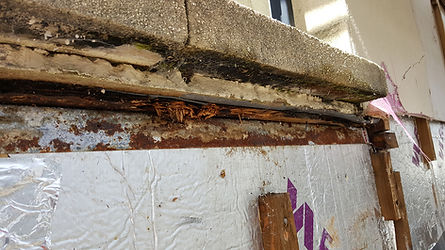


Moisture in the cavity had risen and condensed on the uppermost cold steel
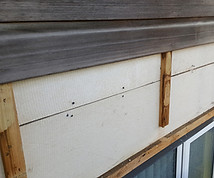
No render or joint sealing behind timber cladding

Our ongoing on-site quality checks identified issues in time to remedy them

Delamination of the render coating from the backer board

Corrosion of the original fixings
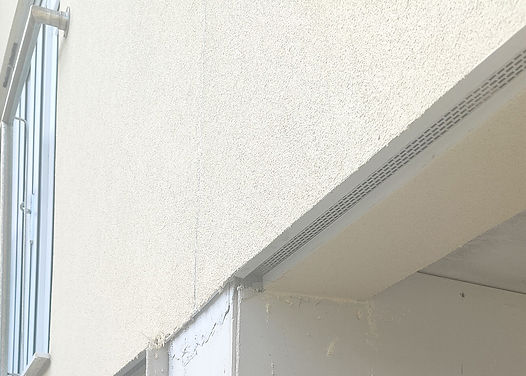
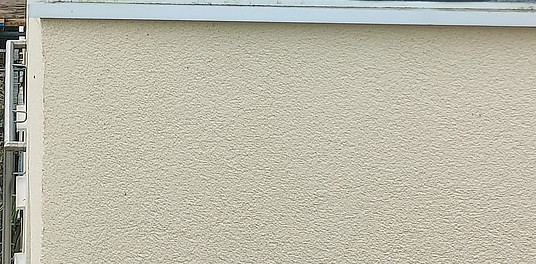
Towards the end of remediation works
After 12 months